Plastic extrusion specialists delivering precision and quality
Plastic extrusion specialists delivering precision and quality
Blog Article
A Comprehensive Guide to the Refine and Benefits of Plastic Extrusion
In the substantial realm of production, plastic extrusion arises as a important and extremely efficient procedure. Translating raw plastic into constant profiles, it accommodates a variety of industries with its remarkable convenience. This overview intends to clarify the elaborate steps involved in this technique, the kinds of plastic proper for extrusion, and the game-changing advantages it offers the industry. The ensuing discussion assures to unfold the real-world influences of this transformative process.
Understanding the Fundamentals of Plastic Extrusion
While it might show up complex at very first glance, the procedure of plastic extrusion is basically simple - plastic extrusion. It is a high-volume production strategy in which raw plastic is melted and formed right into a continuous account. The procedure starts with the feeding of plastic material, in the kind of pellets, granules, or powders, right into a warmed barrel. The plastic is after that thawed utilizing a combination of warm and shear, applied by a turning screw. Once the molten plastic gets to the end of the barrel, it is required with a tiny opening referred to as a die, shaping it right into a wanted form. The designed plastic is after that cooled, strengthened, and reduced into preferred sizes, finishing the process.
The Technical Process of Plastic Extrusion Explained
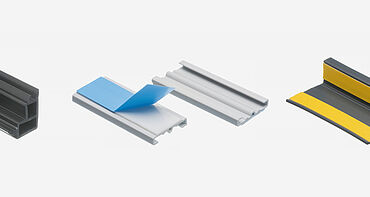
Types of Plastic Suitable for Extrusion
The selection of the ideal sort of plastic is a vital facet of the extrusion procedure. Different plastics provide unique residential or commercial properties, making them a lot more fit to specific applications. Polyethylene, as an example, is frequently utilized as a result of its inexpensive and easy formability. It supplies excellent resistance to chemicals and wetness, making it ideal for items like tubes and containers. Polypropylene is one more prominent option due to its high melting factor and resistance to exhaustion. For more durable applications, polystyrene and PVC (polyvinyl chloride) are typically selected for their stamina and longevity. Although these prevail alternatives, the option ultimately relies on the particular demands of the item being generated. Understanding these plastic types can considerably boost the extrusion procedure.
Comparing Plastic Extrusion to Other Plastic Forming Techniques
Understanding the types of plastic appropriate for extrusion leads the method for a broader conversation on just how plastic extrusion piles up against other plastic forming methods. Plastic extrusion is unrivaled when it comes to developing continuous profiles, such as pipes, gaskets, and seals. It also enables for a constant cross-section along the length of the product.
Secret Benefits of Plastic Extrusion in Manufacturing
In the realm of manufacturing, plastic extrusion uses several substantial benefits. One significant advantage is the cost-effectiveness of the process, which makes it a financially appealing production method. Additionally, this method offers exceptional item versatility and enhanced manufacturing rate, therefore increasing general manufacturing performance.
Economical Manufacturing Approach
Plastic extrusion jumps to the center as a cost-effective production method in production. This process attracts attention for its capability to generate high volumes of product quickly and successfully, giving suppliers with click for info substantial cost savings. The key expense advantage is the capability to make use of much less costly resources. Extrusion utilizes polycarbonate materials, which are less expensive compared to porcelains or metals. Better, the extrusion procedure itself is fairly easy, reducing labor expenses. Furthermore, plastic extrusion requires less energy than typical production techniques, adding to lower operational expenses. The procedure likewise reduces waste, as any excess or defective products can be reused and recycled, offering one more layer of cost-effectiveness. Overall, the monetary advantages make plastic extrusion a very appealing choice in the manufacturing industry.

Superior Item Adaptability
Beyond the cost-effectiveness of plastic extrusion, an additional substantial benefit in making depend on its premium product adaptability. This process enables Resources the development of a large array of products with differing layouts, dimensions, and shapes, from simple plastic sheets to intricate accounts. The versatility is credited to the extrusion die, which can be tailored to yield the wanted item layout. This makes plastic extrusion an ideal option for sectors that need tailored plastic elements, such as vehicle, building and construction, and packaging. The ability to create varied products is not only beneficial in meeting details market demands but likewise in making it possible for suppliers to check out new item lines with marginal capital expense. Fundamentally, plastic extrusion's item flexibility promotes advancement while boosting functional performance.
Improved Production Rate
A considerable benefit of plastic extrusion lies in its improved manufacturing speed. Couple of other production procedures can match the speed of plastic extrusion. In addition, the capability to preserve consistent high-speed production without giving up product high quality sets plastic extrusion apart from various other methods.
Real-world Applications and Influences of Plastic Extrusion
In the world of production, the method of plastic extrusion holds extensive relevance. This process is commonly utilized in the manufacturing of a range of items, such as plastic tubing, window structures, and weather removing. Consequently, it considerably affects industries like building and construction, packaging, and auto sectors. Its effect extends to day-to-day products, from plastic bags to tooth brushes and disposable cutlery. The economic advantage of plastic extrusion, primarily its high-volume and economical output, has revolutionized production. The environmental impact of plastic waste remains a worry. Therefore, the market is persistently striving official website for developments in naturally degradable and recyclable materials, showing a future where the advantages of plastic extrusion can be maintained without jeopardizing ecological sustainability.
Final thought
In final thought, plastic extrusion is a efficient and extremely effective technique of transforming resources into varied products. It supplies many benefits over various other plastic creating methods, consisting of cost-effectiveness, high output, marginal waste, and design adaptability. Its impact is profoundly felt in numerous industries such as building and construction, automotive, and consumer items, making it a crucial procedure in today's production landscape.
Delving deeper into the technological procedure of plastic extrusion, it begins with the option of the proper plastic material. As soon as cooled, the plastic is reduced into the called for sizes or wound onto reels if the product is a plastic film or sheet - plastic extrusion. Comparing Plastic Extrusion to Various Other Plastic Forming Approaches
Understanding the types of plastic appropriate for extrusion leads the method for a more comprehensive discussion on exactly how plastic extrusion piles up against other plastic forming approaches. Couple of other manufacturing procedures can match the speed of plastic extrusion.
Report this page